EVOLVE SmartProfile
GD&T Evaluation Software
EVOLVE SmartProfile® from KOTEM is the world’s leading dimensional analysis software. SmartProfile provides guidance for adding or modifying part design tolerances. It combines measurement data with the CAD model of the part and automatically runs GD&T (ASME) and GPS (ISO) evaluations. Its rich set of tools allow engineers to analyze and solve complex manufacturing problems.
- Eliminate results variability caused by using different evaluation techniques and/or metrology software.
- Eliminate human error caused by incorrect interpretation and implementation of ASME Y14.5 and ISO 1101 standards.
- Quickly assess part tolerances and processes to improve production.
- Optimize enterprise resources by separating part measurements from the tolerance evaluation process.
Easy to Use GD&T Evaluation
SmartProfile makes it easy to set up a new project to analyze product tolerances:
1. Import CAD model
EVOLVE SmartProfile can import industry-standard CAD file formats including STEP, IGES, DXF, and QIF.
CAD models with PMI information can be imported from QIF (Quality Information Framework*) files.
* A unified XML framework standard for computer-aided quality measurement systems enables the import of both CAD model and the PMI (Product Manufacturing Information) learn more.
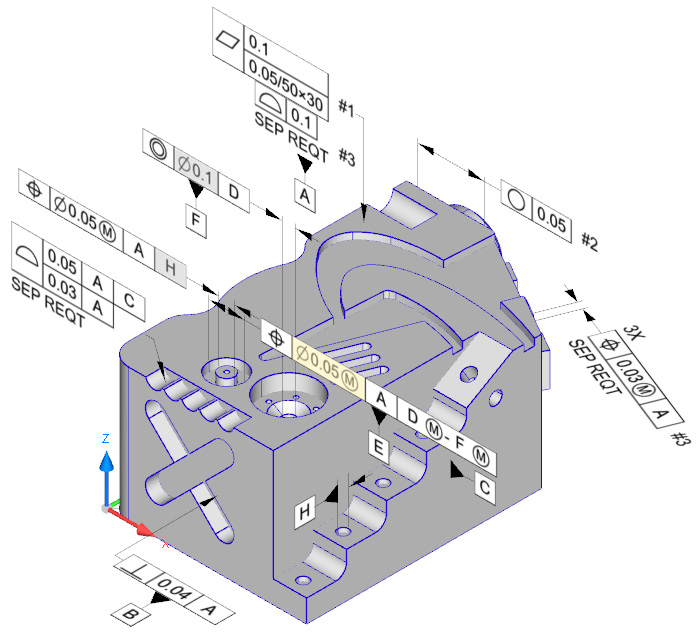
2. Define Tolerances
EVOLVE SmartProfile allows you to define GD&T (GPS) tolerances according to the chosen standard (ASME Y14.5M – 1994, ASME Y14.5 – 2009, or ISO 1101). The built-in Explanatory System always shows relevant information from the current context.
EVOLVE SmartProfile supports enhanced GD&T callouts including: multi-tier tolerances, compound datums and shift, simultaneous & separate requirements, and more.
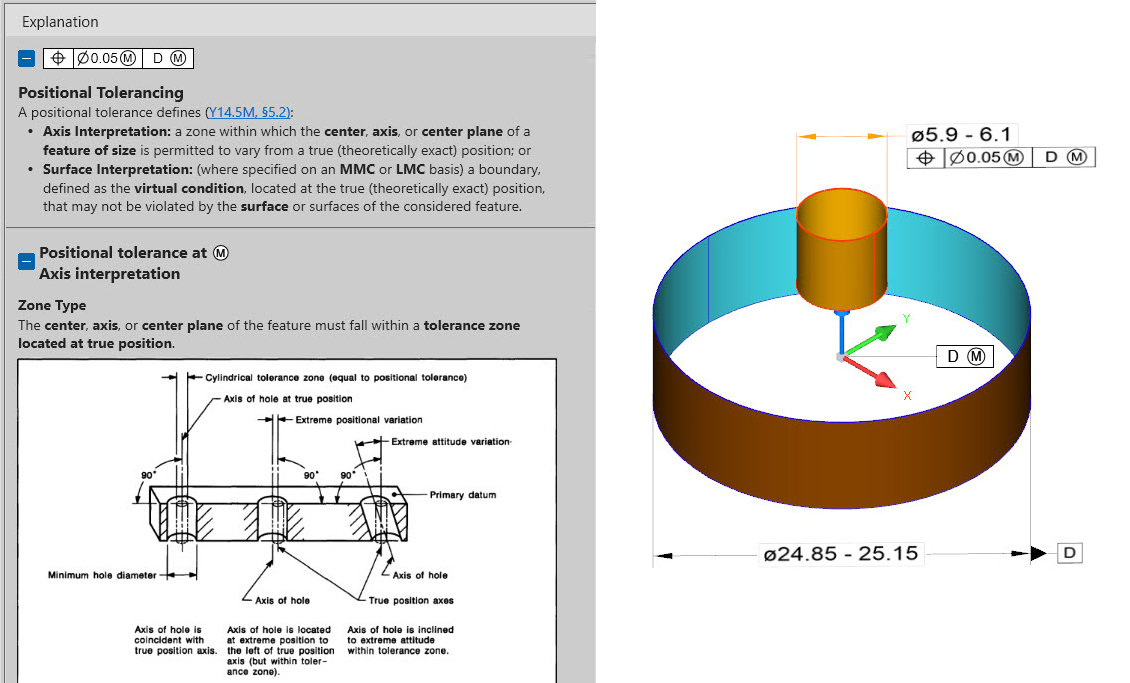
3. Evaluate GD&T
Import measured point clouds from any measuring device: CMM, laser scanner, CT and others. Process large point clouds using the optional Data Preparation tool to speed analysis without loss of analysis integrity.
Evaluate the entire GD&T project with one-click. Using EVOLVE SmartProfile eliminates results variability caused by different evaluation techniques, software algorithms, and human interpretation.
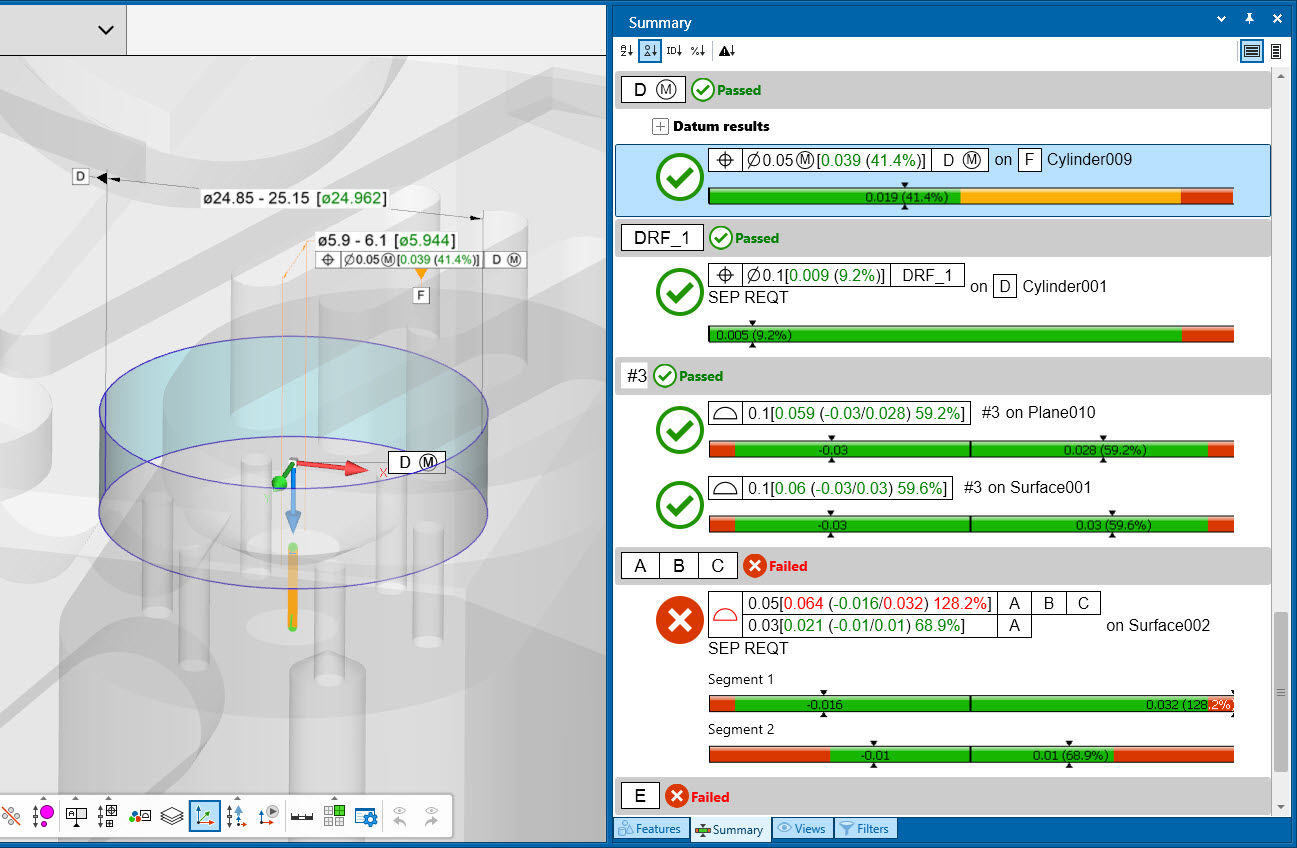
4. Save Results
Custom graphical and text reports are easily created and can be exported into Excel, PDF, text and other file formats.
The project can be saved for future reference and imported into other EVOLVE products.
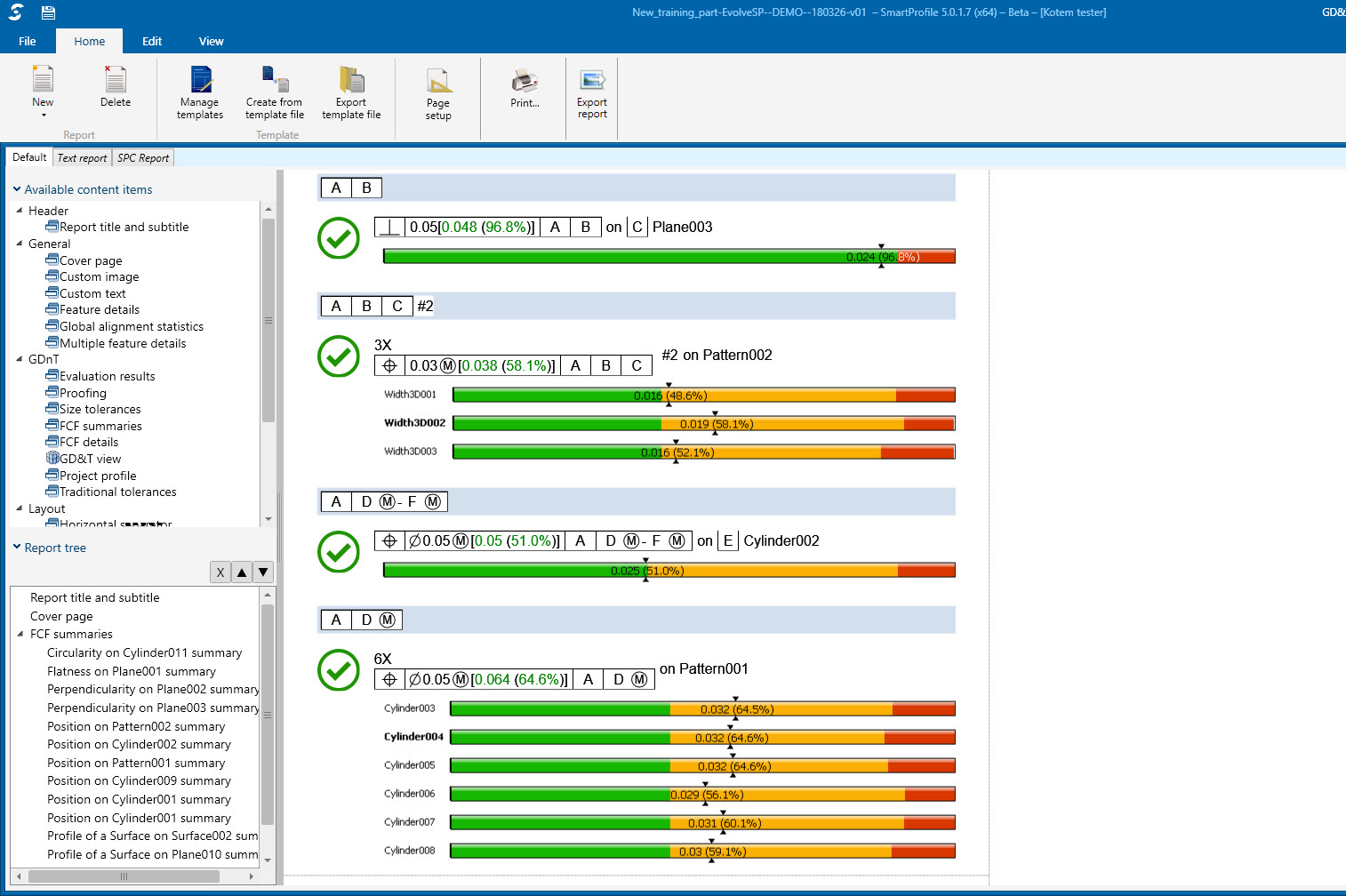
GD&T Standards
The SmartProfile GD&T engine complies with all major GD&T standards (ASME Y14.5M-1994, ASME Y14.5-2009, ISO 1101) as well as Least Squares evaluation. It supports multi-tier tolerances, complex and compound datums and standard symbols in Feature Control Frames.
Data Preparation Tool
The Large Number of Points (LNP) option allows efficient, lossless importing and handling of point clouds with large numbers of points.
Deviation Coloring
Color-coded deviations while processing points allow easy monitoring. Deviation colors are available for source vs. result, and for CAD vs. result.
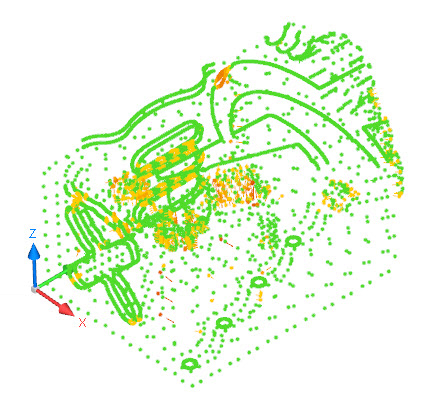
CMM-like Sampler
A CMM-like Sampler tool for extracting reliable representative surface points from dense and noisy point clouds.
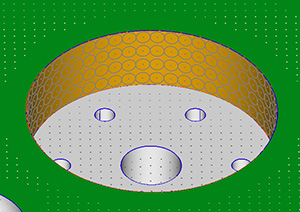
Noise Reduction
Settings for Noise Reduction include surface and curve-based options depending on the point structure.
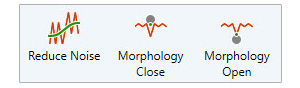
Filter by Deviation
The Filter by Deviation tool eliminates outliers, islands and unnecessary points based on how much they deviate from the CAD model.
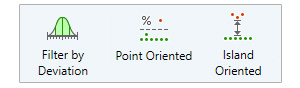
EVOLVE SmartProfile features
Constructions
Construct new features from existing CAD geometries to use as datums or other GD&T/GPS calculations.
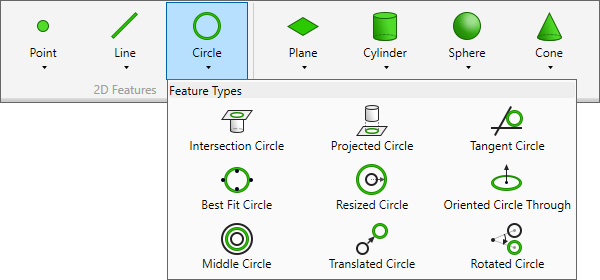
Traditional Tolerances
Define plus-minus distances and angle tolerances between any two arbitrary features.
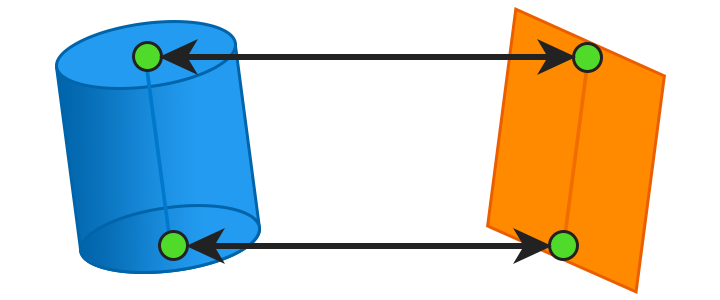
Best-Fit Alignment
Best-Fit Alignment deviation mode supports the ability to visualize sample deviations on a color map, locate deviation labels and document those deviations as part of the completed report.
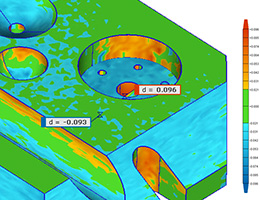
Quick Align
Enhanced Quick Align and Finalize Assignment algorithms automatically detect outliers in the data resulting in a much more robust and proper fit.
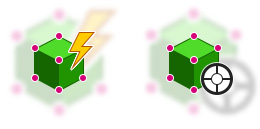
Update Revised CAD Files
Easily replace an old CAD model with a new one. If the CAD model is modified it can be easily updated in the project without the need to create a new project for the new CAD model.