EVOLVE Design
Improves Design GD&T
EVOLVE Design is Computer-Aided Engineering (CAE) tolerancing software that helps engineers apply correct GD&T (GPS) tolerances to their CAD models.
- Apply functionally and syntactically correct GD&T in a 3D model
- Proof your CAD model’s GD&T and get helpful guidance about changes
- Learn from context-sensitive explanations that refer to the specific section of the standards
- Eliminate waste and errors in manual transcriptions of GD&T
Key Features of EVOLVE Design
Easy Workflow
- Import CAD and PMI
- Define Tolerances (import or enter directly)
- Proof project for GD&T (GPS) consistency
- Generate and export PDF report or save your project
EVOLVE Design proofs your GD&T (GPS) tolerances on the model. It highlights potential tolerancing problems and provides recommendations through its explanatory systems that show relevant guidance based on the GD&T standard chosen.
The EVOLVE Design Tolerance Stackup and Point Generator tools allow for a better understanding of the impact of chosen tolerances.
1. Import CAD and PMI
EVOLVE Design imports various CAD file formats including STEP, IGES, DXF, and QIF.
CAD models with PMI information such as GD&T (datums and tolerances) can be imported from QIF (Quality Information Framework*) and STEP 242 files.
* A unified XML framework standard for computer-aided quality measurement systems enables the import of both CAD model and the PMI (Product Manufacturing Information) learn more.
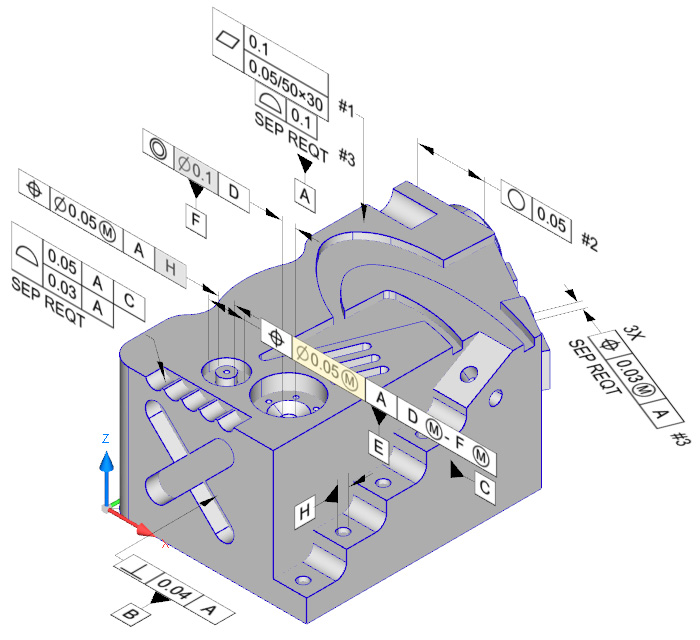
2. Define Tolerances
EVOLVE Design allows you to define GD&T (GPS) tolerances according to the chosen standard (ASME Y14.5M – 1994, ASME Y14.5 – 2009, ASME Y14.5 – 2018 or ISO 1101).
The EVOLVE Design Explanatory System reacts to the state changes in the application and always displays relevant information about the current context.
Explanatory System
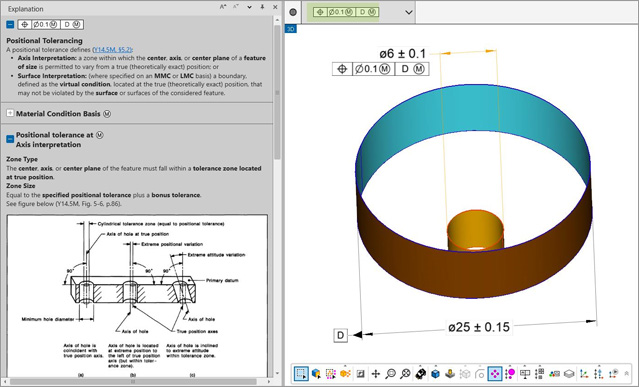
EVOLVE Design has clickable links in the text that open the relevant standard chapter of ASME and ISO (coming soon) standards. The dynamic content is based on the applied modifiers.
- Material condition modifier
- Tangent plane
- Projected tolerance zone
- and more
3. Proof GD&T (GPS)
A powerful GD&T (GPS) engine checks the entire model and provides visual notification of tolerance errors and warnings. The issues found are clearly explained and supported by links to the sections of the relevant standards.
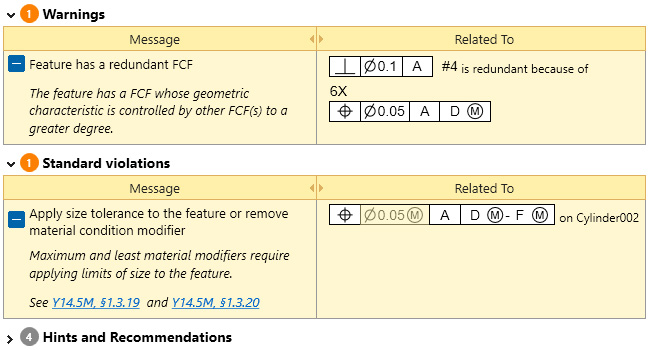
Additional tools: Tolerance Stackup and Point Generator help with better understanding of the impact of chosen tolerances.
Tolerance Stack-up
The ability to calculate the minimum and maximum distances between arbitrary nominal features.
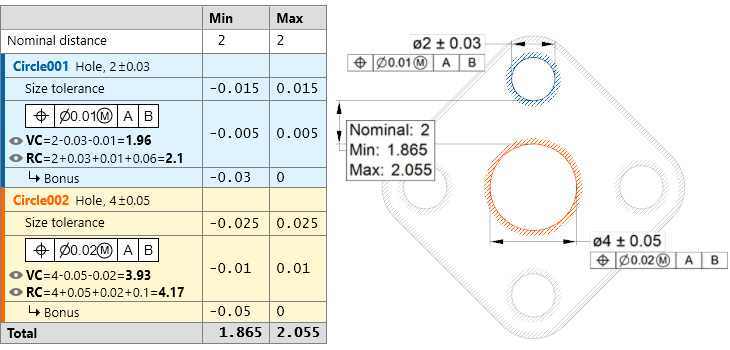
The following parameters influence the results:
- Size tolerance of the selected source features
- GD&T tolerances on the source features
- Bonus tolerance
- MMB datums
- Virtual and Resultant Conditions
Point Generator
Generate virtual parts to perform “what-if” analysis on a single part.
These feature parameters can be changed:
- Actual size
- Translation in chosen Coordinate System (CSYS)
- Orientation in preferred Coordinate System (CSYS)
- Form amplitude
Feature Construction
Construct new features from existing CAD geometries.
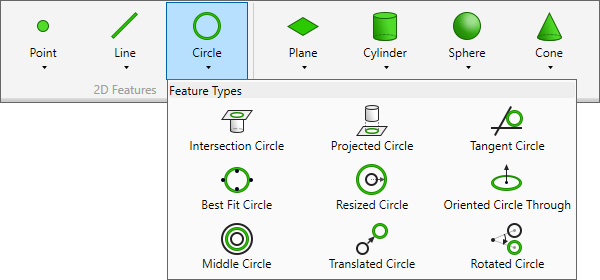
Distances & Angles
Define plus-minus distances and angle tolerances.
- Distance and angle between two arbitrary features can be created
- The angle of the cone can be defined
4. Generate Report or Save to Project file
Reporting
After proofing issues are corrected, the changes to GD&T (GPS) can be saved as a report or a project for future reference and can be imported into other EVOLVE products.
- Create custom graphical reports
- Save template
- Export PDF report
Exporting
EVOLVE Design can be exported to EVOLVE Project files to be used by EVOLVE SmartProfile for part evaluation.